ATNESIS operates at world-class OEE using Monitor MI
The pandemic has sent the manufacturing world into a downward spiral. Manufacturers are facing difficulties in having full control over their machines and overseeing shop floor operations as they are forced to work from home. There is still no way for them to do so even they are allowed to resume operations with a 50% of their production workforce.
As many manufacturers fight to stay afloat, some manufacturing companies have been spared the worst impact of production disruptions in this challenging situation. Mr. CL Neoh, Director of ATNESIS Sdn. Bhd. is the exemplar of manufacturer that comes out of the crisis far more successfully than their peers.
ATNESIS (formerly known as UWC Electric), is an electromagnetic locks manufacturer in Southeast Asia. They were awarded "Best Monitor ERP System Implementation 2018" at the Monitor G5 launch event last year. Let’s see how the bold move they made in deploying Monitor MI one year ago has helped them take control over their production line remotely, improve machines efficiency and operate at high OEE score with just half his workforce during this crisis.
It was almost two months ago since the first phase of the movement control order (MCO) was imposed in Malaysia. Were you allowed to run any operations during this period?
Yes, we were allowed to operate during MCO after the appeal. It is definitely not business as usual, and it came with a lot of frustration as normal things become abnormal. Our focus shifted toward 'how to react to this crisis' - the workforce reduced to half, planning, supply, and shipment disrupted, rescheduling, renegotiating with the customers, and the list goes on.
What was the greatest challenge you faced in running your business during that time?
It was very challenging to run a business in such a situation. The biggest challenge came from how fast our business could adapt to the disruption. This process could take some time, depending on how resilient our business process is.
We are lucky to have embarked on the digital transformation journey two years ago. Now, our staff can work from home - we can plan, execute, and control manufacturing production from home.
While working from home and having your production staff running the production in the factory, had it been difficult to have control over your inventory, production output, work in progress (WIP), finished goods (FG), and deliveries? Which part of the operation did you find the most difficult to manage?
We didn't have much of the above problems as all the data is stored in Monitor ERP. The business processes are well-defined, the workflow is clear, and is available at our fingertips. The most difficult task was the 50% reduction in the workforce.
Tell us how using Monitor Machine Integration (MI) has helped your CNC department and in some other processes during this period.
We have ten machines integrated with Monitor ERP, where data from orders can be connected to the machines and are updated every minute.
We can monitor production data from home, whether a machine stops or runs, causes for machine stop, how many completed or pending orders, what are the next orders to run, and reaching high OEE. This helps a lot in our workforce training and performance evaluation as we are able to respond to hiccups relatively fast.
Moving forward, the need to be able to have control over your business from anywhere will be imperative. How well prepared are you for that, and what future investments are you looking at in terms of technology?
We anticipate more values in the coming future in leveraging the ERP system by integrating more machines and implementing functionalities like Electronic Invoice Management (EIM) and upgrading to MONITOR G5 - working toward smart factory.
Do you have any idea what is the increased efficiency rate after you have implemented MI?
We don’t have an exact figure to tell, but I can share some indications. Initially, when we implement MI, the daily average OEE may be around 50%, and the rate varied a lot from day to day, the fluctuations were huge. We were curious why such variations happened, so we investigated into what causes the fluctuations.
In order to get the OEE score right, so many of our problems surfaced, just to name a few:
- Cumulative stop time was overly long - waiting for materials, frequent change of product model, first piece buy off time, change of tool, cleaning, briefing and meeting time, unplanned machine downtime.
- Poor quality - high rejection rate, workers and leaders' lack of knowledge, inferior materials, or varying lot quality, poor machine conditions.
- Cycle time exceeded - improperly trained workforce, wrong tooling.
Today, our daily average OEE still fluctuates, but with much lower variance with the maximum OEE hitting 94%, which is the light at the end of the tunnel. We are getting closer to achieving a stable OEE score of 85%, the world-class standard.
Our workers are happy because they are given clear instructions and sufficient training, and their efforts are appreciated. Managers can set their priorities well as they know the level of improvement they need; and how they want their leaders to perform.
Personally, I like the idea of MI. When we look at our problem layer by layer, and in a bottom-up way, it makes me rethink how things should be implemented, making things transparent, communication improves, abstract performance quantifiable.
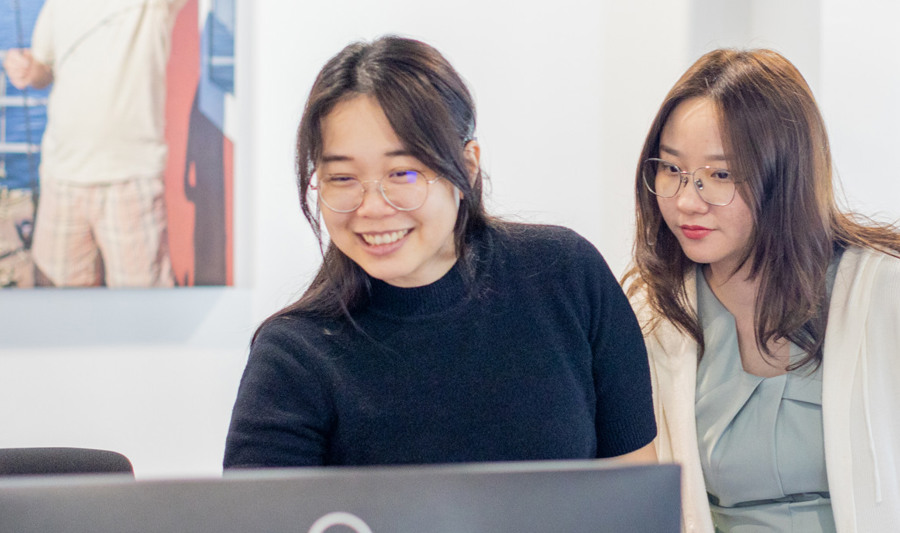