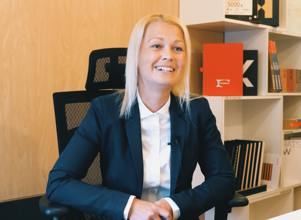
Why Plaat Detail said “No other ERP system could do this"
When Estonian manufacturer Plaat Detail set out to digitalize their entire production, they weren’t looking for just any ERP system, they needed one built for real-time control, automation, and sustainability. No other ERP system in Estonia could deliver what they were looking for. That’s why they chose Monitor ERP.
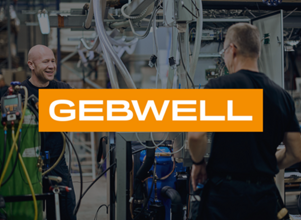
Gebwell Oy switches to Monitor ERP in record time
The ERP system was upgraded to support the company's growth, internationalization and business process development.
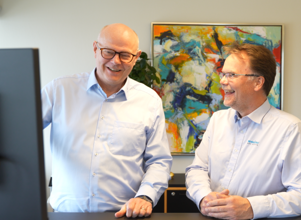
Focus on efficiency and trust: Lind Jensen Maskinfabrik and three years with Monitor ERP
For more than 60 years, Lind Jensen Maskinfabrik, a Danish manufacturing company with global operations including China and India, has delivered quality solutions to a wide range of industries. With more than 100,000 different parts to keep track of, a good ERP system was a necessity. Three years ago, the company decided to switch to Monitor ERP - a decision that has strengthened operations, overview and collaboration across national borders.
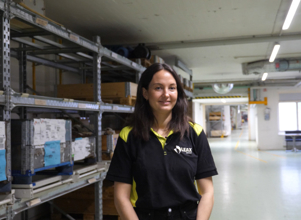
LEAX Skaraborg boosts efficiency with Advanced stock management
When LEAX Skaraborg chose to implement Monitor ERP's Advanced stock management, their daily workflow improved significantly. From manual and time-consuming to efficient and well-structured.
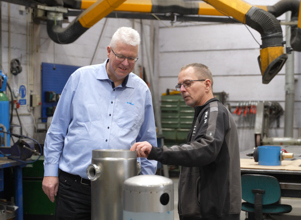
From manual work to digital precision: Winthers Smede Entreprise chooses Monitor ERP
At Winthers Smede Entreprise, it's all about precision, quality, and efficiency. That’s why, in 2023, they decided to implement Monitor ERP – a decision that has made a big difference in their daily operations.
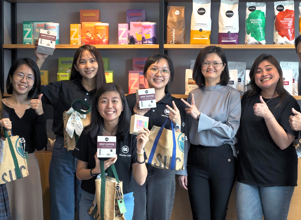
Brewing efficiency and sustainability: Coffex Coffee's journey with Monitor ERP
Coffex Coffee (M) Sdn. Bhd., established in 1997, has been a pioneer in delivering gourmet coffee across the Asia-Pacific region. Under the leadership of CEO, Kelvin Ngow, the company set up a roasting facility in Glenmarie, Shah Alam, to cater to the growing appreciation for exceptional coffee in the region.
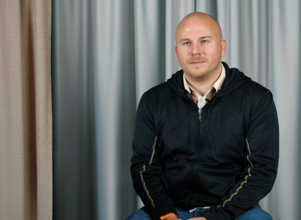
Aura Light reduces their climate footprint thanks to Monitor ERP
With the help of the Sustainability by Monitor function in Monitor ERP, Aura Light has modified the material used in their Helags industrial lighting, significantly reducing their carbon footprint. By changing the material used in production, they have achieved a reduction in carbon emissions by over 45%, leading to an overall decrease of 10% in the product’s total carbon footprint.
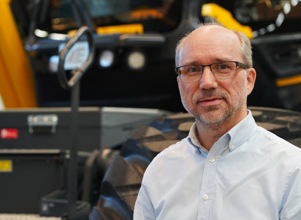
From manual to automated – Eco Log optimizes their processes with PDM integration
For Eco Log, a leading manufacturer of forestry machinery, the pursuit of efficiency and high-quality data led them to implement PDM integration. Thanks to this integration, Eco Log has successfully automated the transfer of data between their product data management (PDM) system and Monitor ERP, eliminating duplication of work and reducing the risk of errors.
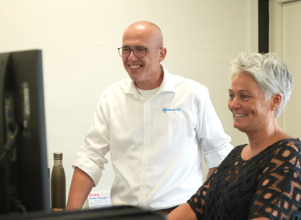
Monitor ERP helps Bjerrum Nielsen boost productivity
Three years ago, the Danish production company Bjerrum Nielsen took a significant step by replacing their previous ERP system, C5, with Monitor ERP. The implementation managed by Monitor, and it has proven to be a right decision for the company, leading to major improvements in their operations.
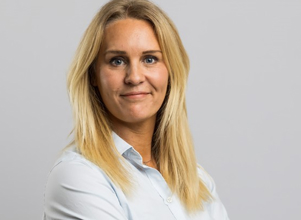
Skotte AB chooses Monitor ERP for its sustainability features
Monitor’s complete ERP system and its sustainability functionality were key factors in Skotte AB’s decision to select Monitor as their new ERP system. Skotte AB offers a wide range of products optimized for their customers across multiple industries, from product owners to contract manufacturers. Their focus is on identifying the best manufacturing methods and processes to maximize efficiency and ensure products of the highest quality.
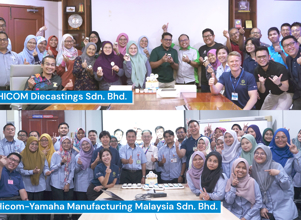
Unified growth: DRB-HICOM's transformation across three companies with Monitor ERP
DRB-HICOM's subsidiaries, HICOM Diecastings Sdn. Bhd., Hicom-Yamaha Manufacturing Malaysia Sdn. Bhd., and HICOM-Teck See Manufacturing Malaysia Sdn. Bhd. have successfully gone live with Monitor ERP, marking a significant milestone in their operational journey.
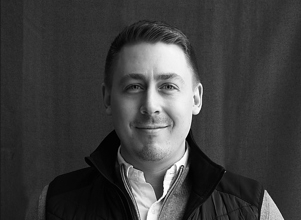
Nordmount’s success with Monitor ERP sets a new standard in the solar panel industry
The Swedish company Nordmount has established itself as a leader in designing solar panel mounting systems. Produced in Sweden with a focus on simple, efficient, and safe solutions, they have gained the trust of installers and raised the standard for rooftop installations. Nordmount’s commitment to quality ensures excellent results for those who live and work under their installations.
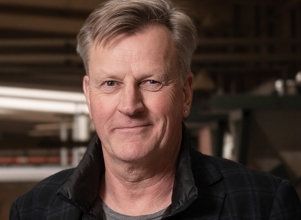
Ifö Electric chooses Monitor ERP for its cost-effectiveness, strong reputation, and extensive functionality
After a careful evaluation, Ifö Electric, a manufacturer of Diazed fuse links, distribution cabinets, lighting, and various low and high voltage fuse links and accessories, has chosen Monitor ERP as their new ERP system. The system’s cost effectiveness, solid reputation, and extensive functionality were key factors in the decision.
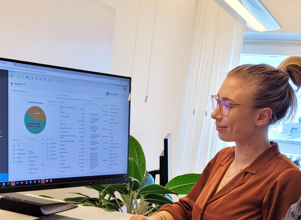
Koenigsegg sees the many advantages of Monitor BI
Koenigsegg regards Monitor BI as a powerful tool that can quickly give them an overview of their data, while also being able to provide detailed reviews in the same dashboard. Monitor BI’s ability to present digestible data to the whole organization and its self-instructional dashboards are what Koenigsegg considers to be the most significant advantages.
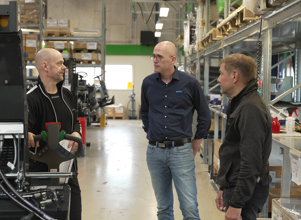
A successful collaboration – Monitor visits Egholm A/S
Implementing a new ERP system is a significant undertaking, especially when faced with the limitations of an outdated ERP system. Egholm A/S recognized the need for new opportunities and chose Monitor ERP. Thanks to a super-committed, pragmatic, and independent project team, Egholm reached the finish line with a successful project, reaping the benefits even a year later. Today, Monitor ERP provides invaluable insights into the company's processes, while the Product configurator has been a great help in creating customer-specific orders.

Sanwa Group's digitalization for traceability and zero defects
Sanwa Group, a pioneer in plastic engineering since its establishment in 1977, has embarked on a digital transformation journey to meet the evolving demands of Industry 4.0. With operations across Asia, including China, India, and Indonesia, the company has consistently pushed the boundaries of excellence to meet the dynamic demands of various industries.
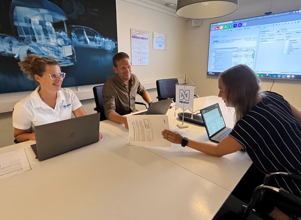
Nitator works greener with Sustainability by Monitor
To take their sustainability efforts a step further, Nitator, a prominent player in the automotive industry and a comprehensive supplier of sheet metal components, has begun using Monitor ERP's environmental feature – Sustainability by Monitor. Sustainability by Monitor is an environmental tool that helps companies to accurately measure their environmental impact and implement sustainability measures.
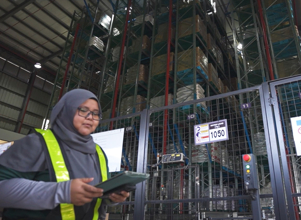
Synerchem Group transforms manufacturing efficiency with Monitor ERP
In the competitive landscape of manufacturing, seamless integration and efficient management systems are paramount for success. Synerchem Group, a leading player in the food industry, recognized this need and embarked on a transformative journey with Monitor ERP.
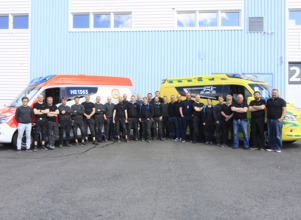
How Monitor ERP helps J5L-Production Oy with their sustainability
To strengthen its position in sustainability and the rapidly evolving business world, the Finnish company J5L-Production Oy, which manufactures specialist vehicles, realized it needed a new, powerful ERP system. After careful consideration they chose Monitor ERP.
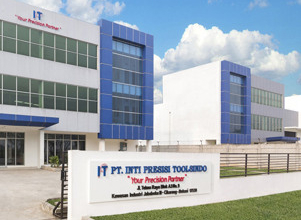
Upgraded to Monitor G5 within one month, and 100% online
Find out what Mr Lim, Director of PT. Inti Presisi Toolsindo (PT Inti), thinks about Monitor G5 and his experience of the upgrade process. PT Inti in Jakarta has been using Monitor ERP since 2015 and provides high-quality, custom-designed precision carbide tools for the aerospace, electronics, oil & gas, and automotive industries. The name PT Inti is currently synonymous with the highest quality. The company has now upgraded to Monitor G5, with the entire process, including training, taking place 100% remotely.
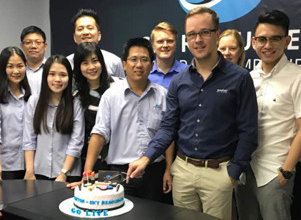
Business as usual for Sky Resources amid the pandemic
“We are using the Sales Forecast function to simulate the quantity and cost required in the next one or two months. This gives us foresight in our cash flow management. It also allows us to bargain for volume discount for the most consumed materials." - Mr. Lee Poh Seng, Purchase Manager at Sky Resources.
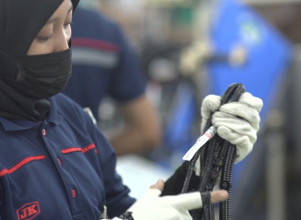
Together we achieve more with J.K. Wire Harness
In conjunction with MIDA-P2 (Malaysian Investment Development Authority) Digital Transformation Ecosystem Programme, J.K. Wire Harness Sdn. Bhd. (JKWH) has digitally transformed its business operations and processes. In order to propel to the forefront of IR4 (Industrial Revolution), JKWH needs a complete ERP system that consolidates all their business processes into one single system. With the successful implementation of Monitor G5, JKWH has improved the efficiency of its business processes.
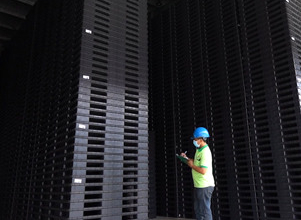
One step closer to becoming a SMART Factory
Mah Sing Plastics Industries Sdn. Bhd. is one of the largest high-tech plastic product manufacturers in Malaysia since its incorporation in 1979. A wholly owned subsidiary of Mah Sing Group Bhd., the company is listed on the main board of Bursa Malaysia. The company supplies plastic products such as pallets, containers, boxes, furniture and more.
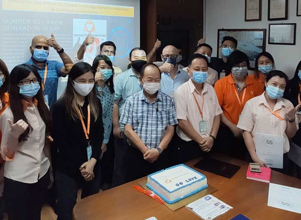
First Malaysian customer grows stronger with G5
Prestige Dynamics Industries Sdn. Bhd. (PDI) has over three decades of experience in precision injection moulding. They have a 10,000 square meter manufacturing plant in Penang, Malaysia with approximately 350 employees.
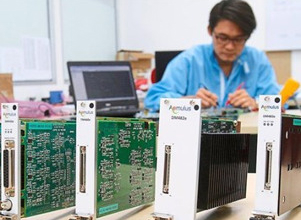
A new level of efficiency at Aemulus corporation – "Worth every single sen"
Aemulus Corporation Sdn. Bhd. designs, engineers, and develops automated equipment which tests the functionality of semiconductor devices. Its equipment is used to test functionality such as power levels, electrical behavior, analog and digital signals, and radio frequency signals. The company was founded in 2004 and is based in Penang, Malaysia.
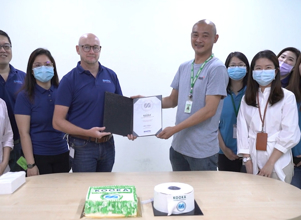
Kooka Paper successfully goes live with Monitor G5 in three weeks
July 8 marked the successful implementation of Monitor ERP system within three weeks at Kooka Paper Manufacturing Sdn. Bhd.
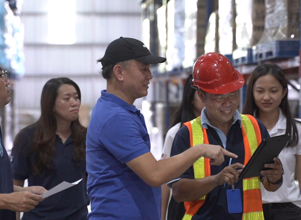
Readycare's key ingredient for automation success - Monitor's Machine Integration (MI)
At the heart of Malaysia's manufacturing landscape, Readycare Manufacturing Sdn. Bhd. stands as a testament to the transformative power of Monitor ERP and MI (Machine Integration).

Gränsfors Bruk now runs Monitor G5 – “The upgrade was seamless”
Gränsfors Bruk now runs Monitor G5 – “The upgrade was seamless”
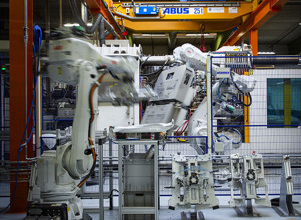
Why KB Components went for Monitor ERP
For Swedish manufacturer KB Components, changing to Monitor ERP means new opportunities, both now and in the future.
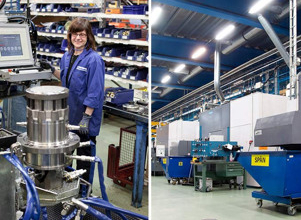
Monitor G5 the logical choice for Indexator
The group includes four other companies which have all run Monitor for several years, so when it was time to change ERP system, the choice was simple.
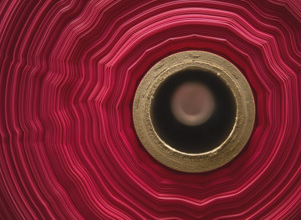
Alfapac chose Monitor ERP to pinpoint production
According to Financial Manager Marcus Kindevåg, Monitor is clearly a system designed for manufacturing companies. "There’s a depth to the system which we can utilize when following up our production, and in reports.”
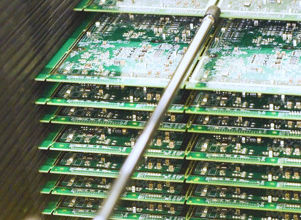
Monitor improves Darekon's supply chain management
Join us on our tour of Darekon’s facilities, get a glimpse of their day-to-day work and see how Monitor ERP makes life easier for Darekon’s employees.
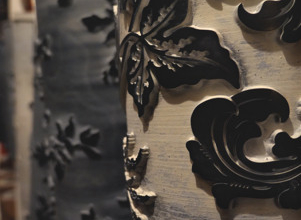
Duro steps up production with Monitor ERP
To handle a larger process flow, we needed an ERP system that was efficient, and wouldn’t cost administrative time. And we chose Monitor ERP.
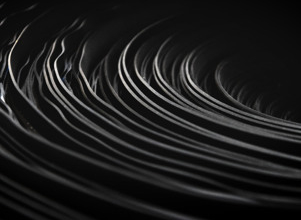
More efficient manufacturing with Monitor G5: “A real boost”
National Halmstad needed a more standardized ERP system which could help it achieve its goal – a digitalized, effective process flow throughout the factory. So it chose Monitor G5.
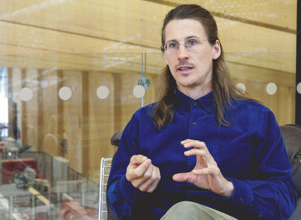
Becoming the world’s greenest furniture company – with Monitor ERP
The Norwegian company Vestre has gone through a lot over its 75 years. Its current focus is to be “the world’s most environmentally friendly furniture manufacturer”.
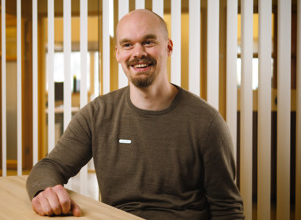
Project-based manufacturing with Monitor ERP
C&D Snickeri is a manufacturer of wood interiors. Each new customer means a new project with new products. “It's important for us that the ERP system can manage the rapid flow of parts and products that pass through our doors,” explains site manager Emil Carlson.
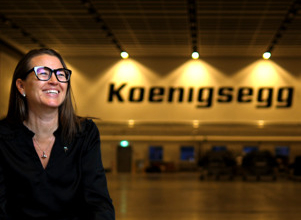
The key to a successful upgrade
With new car models and new factories in the pipeline, Koenigsegg needed a new ERP system. An upgrade is a major project. But Koenigsegg swiftly moved through the gears.
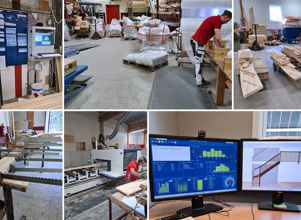
Monitor ERP – a savior in times of need for Olssons Trappor
After a year of pandemic and uncertainty, co-owner Kim Olsson talks about the company’s rewarding journey with Monitor.